In den letzten Jahren hat die additive Fertigung (Additive Manufacturing) den Bereich der Fertigung revolutioniert. Angezogen von den verschiedenen Vorteilen, insbesondere den unzähligen Designmöglichkeiten, die die additive Fertigung bietet, übernehmen immer mehr Branchen diese Technologie. Die Luft- und Raumfahrtindustrie und die biomedizinische Industrie waren die ersten, die diese sich schnell entwickelnden Technologien übernommen haben. Heute kann man bereits mit Flugzeugen fliegen, die über mehrere additiv gefertigte Komponenten verfügen, oder ein speziell für den eigenen Körper entwickeltes Implantat selbst ausdrucken.
Einer der Hauptanziehungspunkte der additiven Fertigung ist, dass sie ein kleiner Teil eines größeren Ganzen ist – der INDUSTRIE 4.0. Die additive Fertigung hilft der Industrie dabei, dem Slogan „Massenproduktion von kundenspezifischen Gütern“ gerecht zu werden. Sie begann als Technologie zur schnellen Erstellung von Prototypen und hat mittlerweile ihren Platz in der täglichen Fertigung gefunden. Im Gegensatz zur subtraktiven Fertigung, bei der Designänderungen kostspielig sind, bietet sie eine einfache Möglichkeit, das Design jedes hergestellten Teils bei Bedarf zu ändern und zu verbessern. Es genügt, das Design des virtuellen Modells des hergestellten Teils anzupassen. Diese direkte Verbindung zwischen der virtuellen Software und den physischen Maschinen macht sie zu einem wertvollen Bestandteil der INDUSTRIE 4.0.
Angesichts der großen Zahl von Maschinenherstellern und kommerziellen Verfahren ist die Nomenklatur der additiven Fertigungsverfahren für Metalle mehrdeutig. Dennoch kann man alle Verfahren in einige Kategorien einteilen.1
1_ Milewski, J. O. (2017). Additive manufacturing of metals. From Fundamental Technology to Rocket Nozzles, Medical Implants, and Custom Jewelry,134-157.
Metallografie für die Additive Fertigung
Inhaltsverzeichnis

Hauptkategorien der bestehenden additiven Fertigungsverfahren für Metalle.
Auch wenn es einfach klingen mag, ist der Forschungsaufwand, den die additive Fertigung erfordert, um die Qualität einer Fertigung zu gewährleisten, enorm. Während technische Normen verfasst und ständig weiterentwickelt werden, ist die additive Fertigung extrem flexibel und designabhängig, wobei eine Vielzahl von Maschinenparametern eine Rolle spielt. Zu den vielen Parametern, die die endgültigen Eigenschaften beeinflussen, gehören :
- Chemie der Pulver
- Form und Größe der Pulver
- Verwendete Technologie und Maschinenmodell
- Eigenschaften des Laserstrahls – Form und Leistung in laserbasierten Prozessen
- Eigenschaften des Elektronenstrahls – Stärke und Stärke in elektronenbasierten Prozessen
- Ausrichtung der Konstruktion
Es ist wichtig, den Einfluss all dieser Parameter auf die Mikrostruktur eines Materials zu verstehen, um die Technologien der additiven Fertigung optimal nutzen zu können. Die Mikrostruktur von additiv hergestellten Materialien kann sich stark von der Mikrostruktur konventionell hergestellter Materialien unterscheiden. Dies führt häufig zu einer Verbesserung der mechanischen Eigenschaften. Auf dieser Seite finden Sie eine Fallstudie zur Untersuchung der Mikrostruktur eines additiv hergestellten Materials.
1/ Metallographie
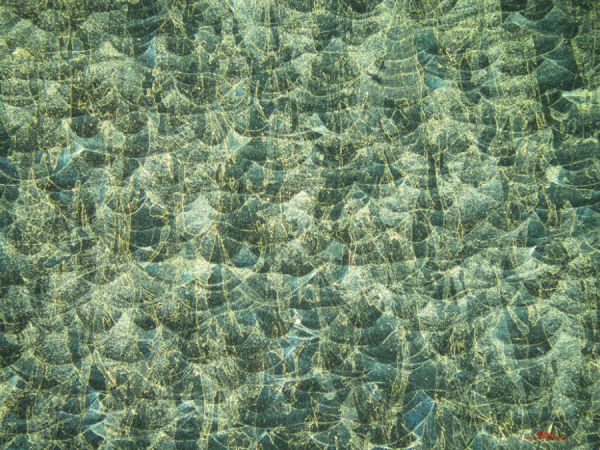
Da die Mikrostruktur direkt die mechanischen Eigenschaften des fertigen Teils bestimmt, ist es wichtig, den Einfluss aller Maschinenparameter auf die Mikrostruktur zu charakterisieren und die Eigenschaften des Pulvers zu kennen. Beispielsweise kann die Herstellungsrichtung die Eigenschaften eines Teils verändern, da die Körner entlang einer Achse säulenförmig angeordnet sein können oder es zu einer Segregation von Ausscheidungen wie Karbiden (in rostfreien Stählen) entlang der Schmelz-/Sinterbahnen kommen kann. Daher untersuchen Metallurgen in vielen Fällen die Mikrostruktur sowohl in Längs- als auch in Querrichtung zur Herstellungsrichtung.
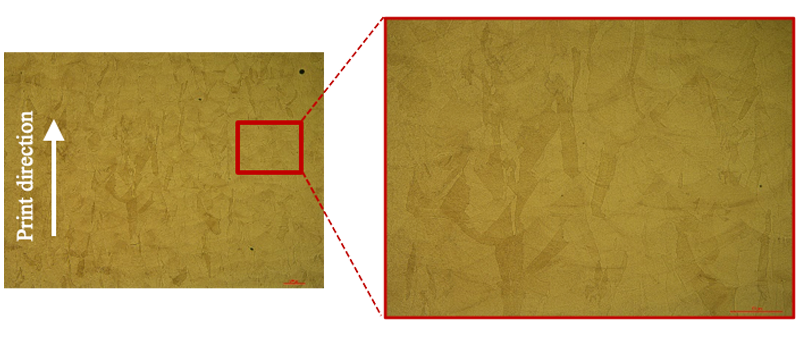
Mikrostruktur in Druckrichtung, die das charakteristische Wellenmuster der geschichteten Pulverschichten zeigt, die beim Ätzen mit Kalling’s Reagenz miteinander verbunden wurden. Es ist zu erkennen, dass die austenitischen Körner in Druckrichtung verlängert sind.
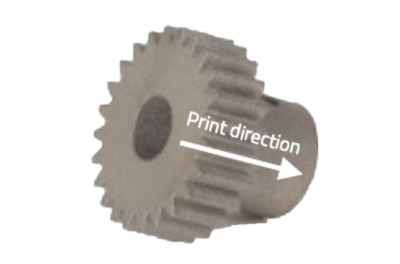
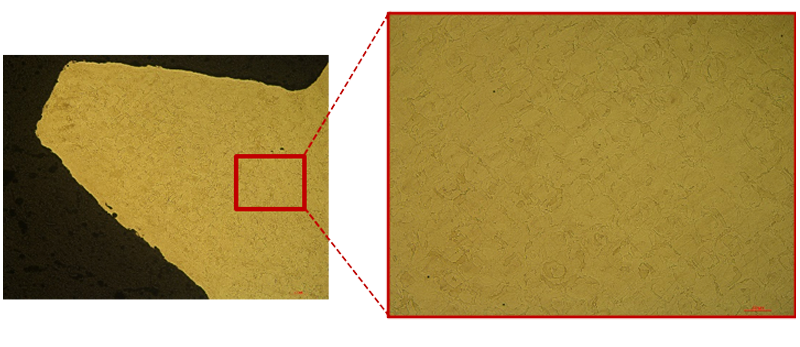
Die Mikrostruktur senkrecht zur Druckrichtung zeigt im Gegensatz zur Druckrichtung mehr gleichachsige austenitische Körner. Aufgrund eines solchen Unterschieds in der Kornmorphologie in verschiedenen Richtungen sind unterschiedliche mechanische Eigenschaften in den beiden Richtungen zu erwarten.
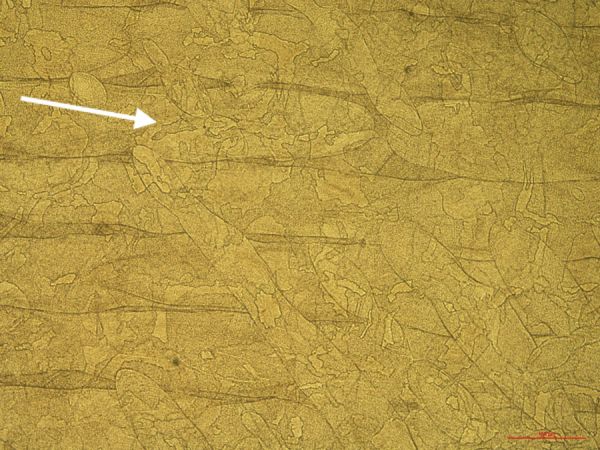
Schmelzspuren des Pulvers (Schmelzspuren) aus dem Lasersintern, die nach dem Ätzen beobachtet werden.
Wie andere konventionelle Fertigungsverfahren ist auch die additive Fertigung anfällig für Fehler. Wenn man die Vorteile der Komplexität des Designs berücksichtigt, sind angemessene Studien erforderlich, um einen Fehler für ein bestimmtes Design, das aus einem bestimmten Prozess hervorgeht, statistisch vorherzusagen. Zur Charakterisierung von additiv gefertigten Teilen wurden zahlreiche verfügbare Normen entwickelt. Allerdings gibt es derzeit keine angemessenen Normen, um Porositäten quantitativ zu klassifizieren. Die Industrie verfasst ihre eigenen Standards zur Qualifizierung von Teilen, da Porositäten stark vom Design abhängen können. Das Design des Teils kann entweder zu einem Unterschmelzen oder einem fehlenden Aufschmelzen des Pulvers führen, die beide Porositäten erzeugen können.
Je nach Design und Prozessparametern sind verschiedene Arten von Porositäten zu erwarten: Gasporosität, Schlüssellochporosität und Schmelzmangel. Porositäten können auch in lokalisierten Bereichen auftreten: an der Oberfläche, unterhalb der Kontur oder in der Masse. Die Industrie entscheidet sich häufig für das HIP-Verfahren (Hot Isostatic Pressing), um Porositäten bis zu einem gewissen Grad zu beseitigen.
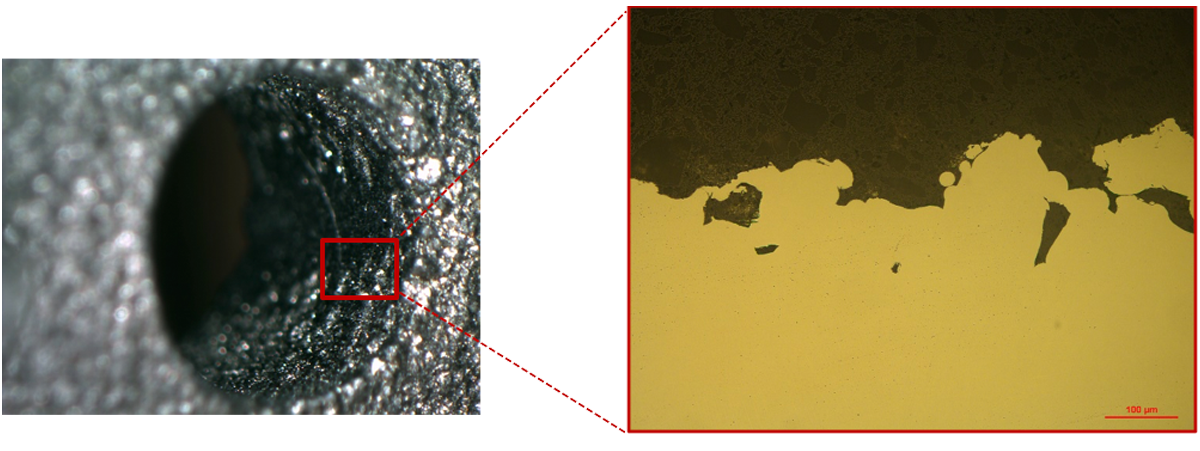
Mikrostruktur entlang der Wände eines hohlen Elements auf einem additiv gefertigten Ti-6Al-4V-Titanteil, die eine schlechte Pulverschmelze zeigt.
Die oben dargestellten Fehler können durch Oberflächenbehandlungen nach dem Prozess beseitigt werden. Gefährlicher sind Defekte in der Masse des gefertigten Teils. Die folgende Abbildung zeigt einen klassischen Defekt, der durch eine schlechte Verschmelzung zwischen den Pulverschichten entsteht. Dies kann auf das Einfangen von Gasen oder Oxideinschlüssen während des Druckvorgangs zurückzuführen sein.
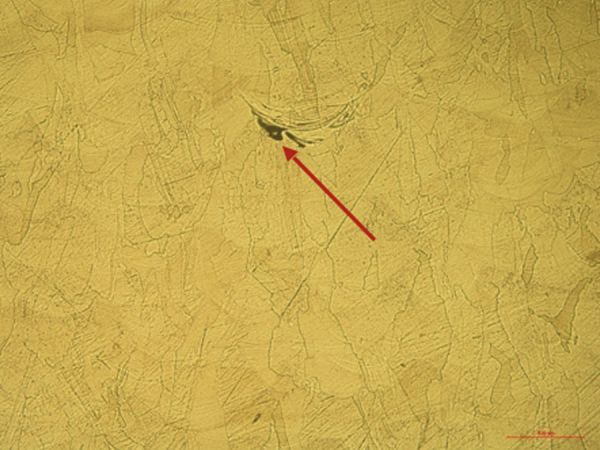
Mikrostruktureller Defekt (roter Pfeil) aufgrund einer schlechten Schichtverschmelzung in einem additiv hergestellten Stahl aus der Legierung 316L.
2/ Methode zur Vorbereitung von Proben
Um die Mikrostruktur zu analysieren, muss die Probe präpariert werden, ohne die Mikrostruktur zu beschädigen. Im Folgenden finden Sie Methoden, die bei jedem Schritt der Probenvorbereitung befolgt werden müssen, um die Mikrostruktur korrekt zu analysieren.
- Trennen
- Einbetten
- Polieren
Trennen
Bei der Vorbereitung einer metallografischen Probe eines additiv gefertigten Teils müssen die interessierenden Regionen richtig ausgewählt werden. Sobald die Region ausgewählt ist, können die Schneidzusätze, die Maschine und die Haltesysteme richtig ausgewählt werden. Häufig sind mehrere Schnitte erforderlich, um die Region of Interest (zu untersuchender Bereich) abzutrennen.
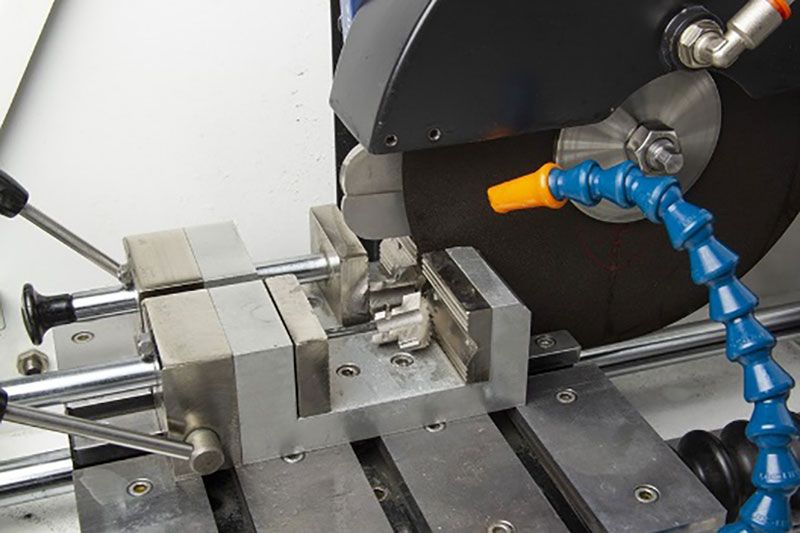
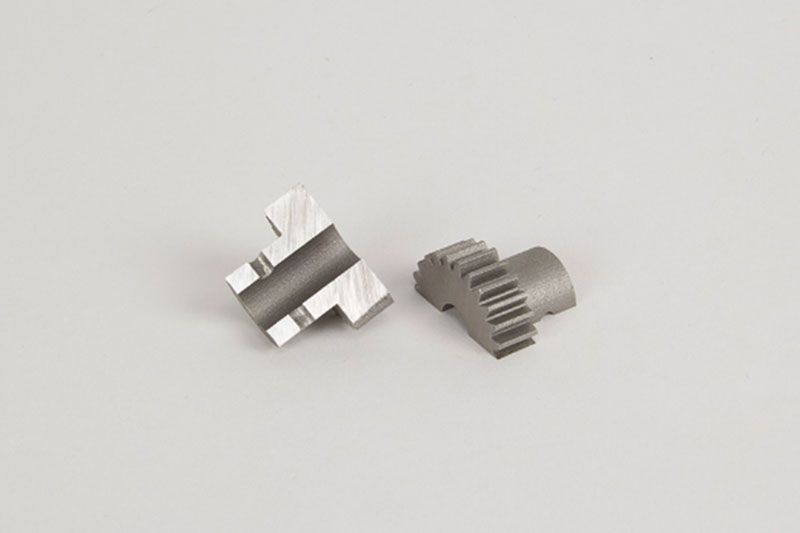
Mit dem 3D-Drucker hergestelltes Teil (Stahl 316L), das mit der roten LAM PLAN Präzisions-Trennscheibe im Bereich von Interesse – Loch senkrecht zur Zahnradachse – geschnitten wurde.
Trennscheibe
Für schnelle Schnitte können die Excellence LAM PLAN-Trennscheiben verwendet werden. Für Präzisionsschnitte werden die LAM PLAN Precision-Trennscheiben empfohlen. Weitere Tipps zu Verbrauchsmaterialien und Schnittparametern finden Sie in unseren Artikeln zur Metallografie von zu trennenden Materialien.
Fixierung
Je nach Form und Größe des Teils muss ein geeigneter Schraubstock oder ein Fixierungssystem ausgewählt werden. Die komplexen Formen von Teilen aus der additiven Fertigung können diesen Prozess zusätzlich erschweren. Die Fixierung von LAM PLAN verhindert übermäßige Vibrationen und das gefährliche Lösen der Teile von den Fixiersystemen beim Schneiden mit Cutlam-Maschinen.
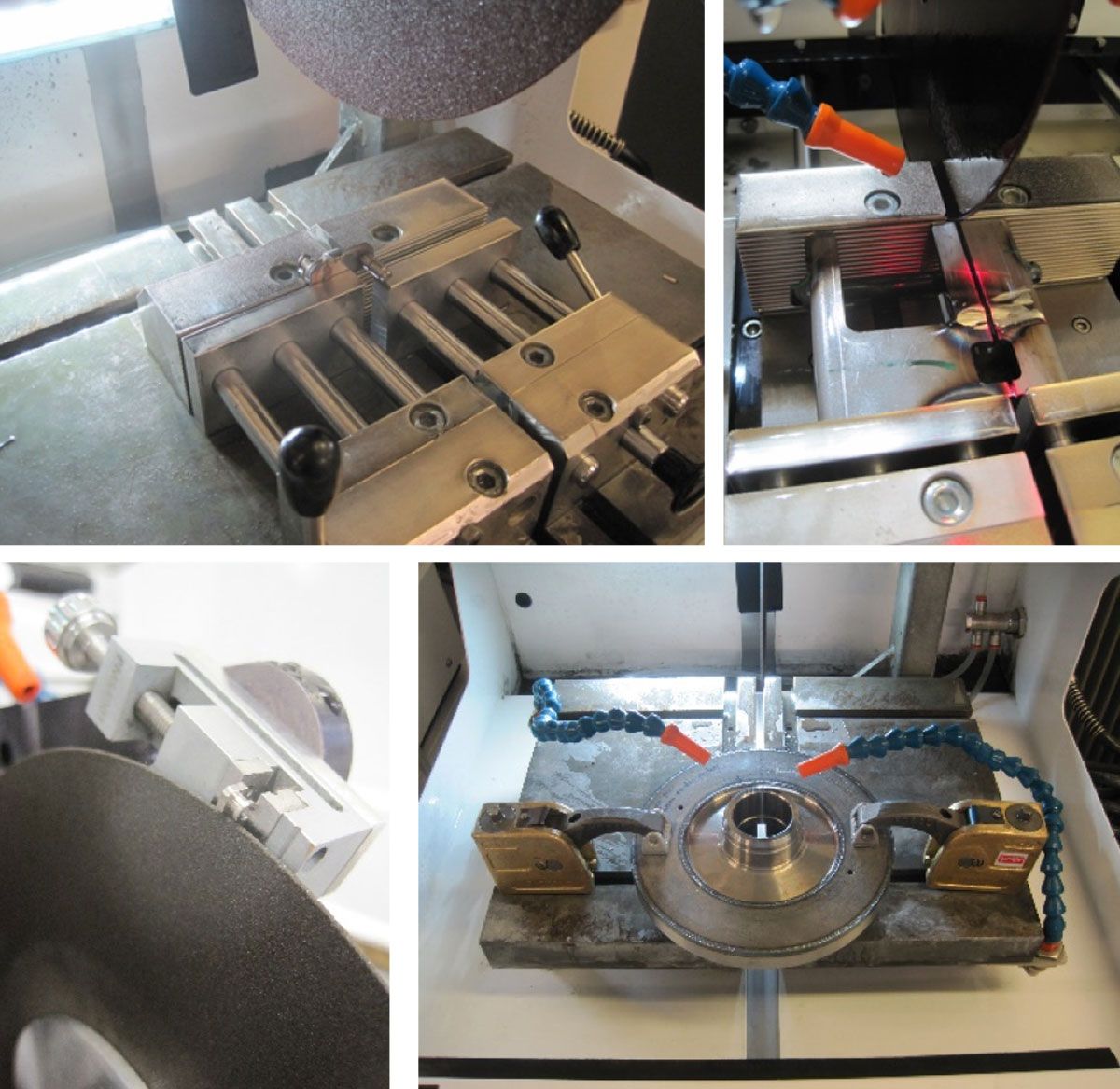
Flüssigkeit zum Trennen
Für Eisenlegierungen wird die Verwendung des Trennfluids LAM PLAN 722 empfohlen, um eine übermäßige Erwärmung und eine Verformung der Mikrostruktur zu vermeiden. Dieses Fluid bietet das richtige Verhältnis von Schmierung und Kühleffekt und ist daher ideal für metallografische Anwendungen.
Zum Trennen von Nichteisenlegierungen sollte das Schneidfluid LAM PLAN 723 verwendet werden.
Einbetten
Additiv gefertigte Teile, die Temperaturen von über 180 °C standhalten, werden mithilfe einer Einbettungspresse heiß mit Harzen eingebettet. Phenolharze bieten Lösungen zum schnellen Einbetten. Wenn jedoch die Analyse der Probenränder kritisch wird, sind Epoxidharze wie Harz 633 oder Harz 634 eine ausgezeichnete Wahl. Diese Epoxidharze haben eine sehr geringe Schrumpfung, wodurch kein Spalt zwischen dem eingebetteten Teil und dem Harz entsteht. Dieses Fehlen eines Zwischenraums verhindert auch die Kreuzkontamination von Schleifmitteln zwischen den Polierschritten. Da sie außerdem das Durchsickern des Ätzmittels verhindern, bieten sie eine hervorragende Lösung für ein gleichmäßiges Ätzen.
Wenn die Teile nicht hocherhitzt werden können, z. B. wenn sie aus Aluminium bestehen, ist das Einbetten im kalten Zustand (bei Raumtemperatur) vorzuziehen. Die weit verbreiteten CMR-freien 605-Harze von LAM PLAN können schnelle Einbettungslösungen bei Raumtemperatur bieten, die zudem einfach zu handhaben sind. Wenn die Kantenschrumpfung kritisch wird, funktionieren das Polyesterharz 607 oder die Epoxidharze 603 und 603.2 effektiv.
Erfahren Sie mehr über unsere Verbrauchsmaterialien zum Einbetten :
Polieren
Zum Schleifen und Polieren können die für konventionell hergestellte Materialien empfohlenen Poliermethoden verwendet werden. Im Folgenden finden Sie verallgemeinerte Poliermethoden, die bei additiv gefertigten Aluminium-, Titan- und Stahllegierungen effektiv funktioniert haben.
Aluminiumlegierungen
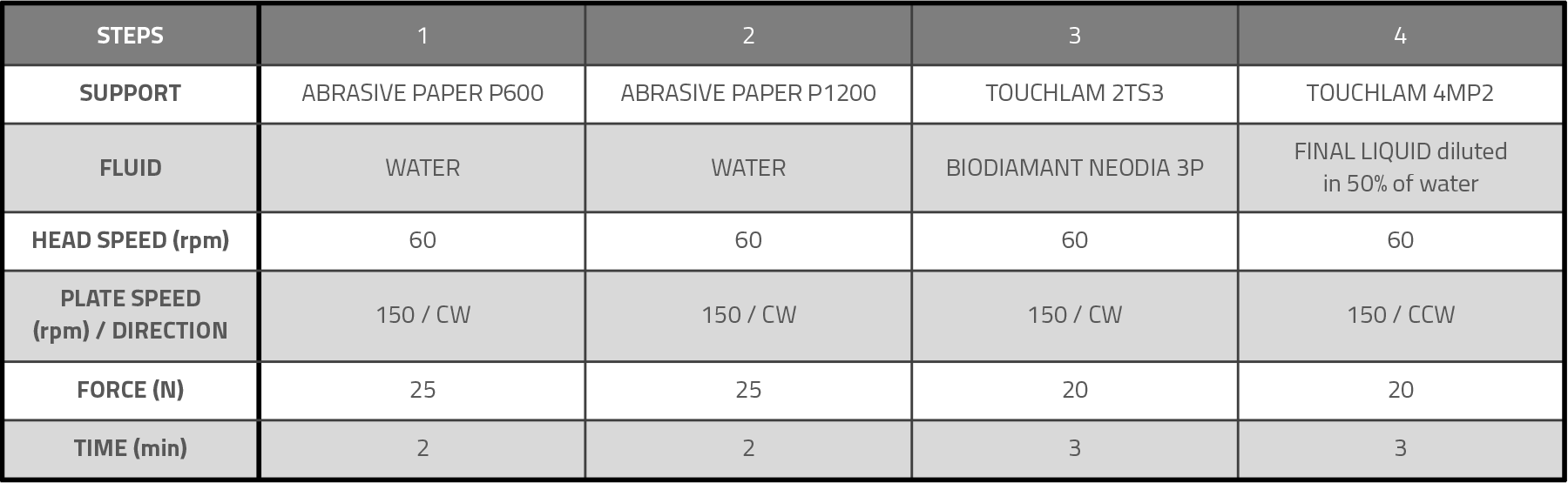
Titanlegierungen
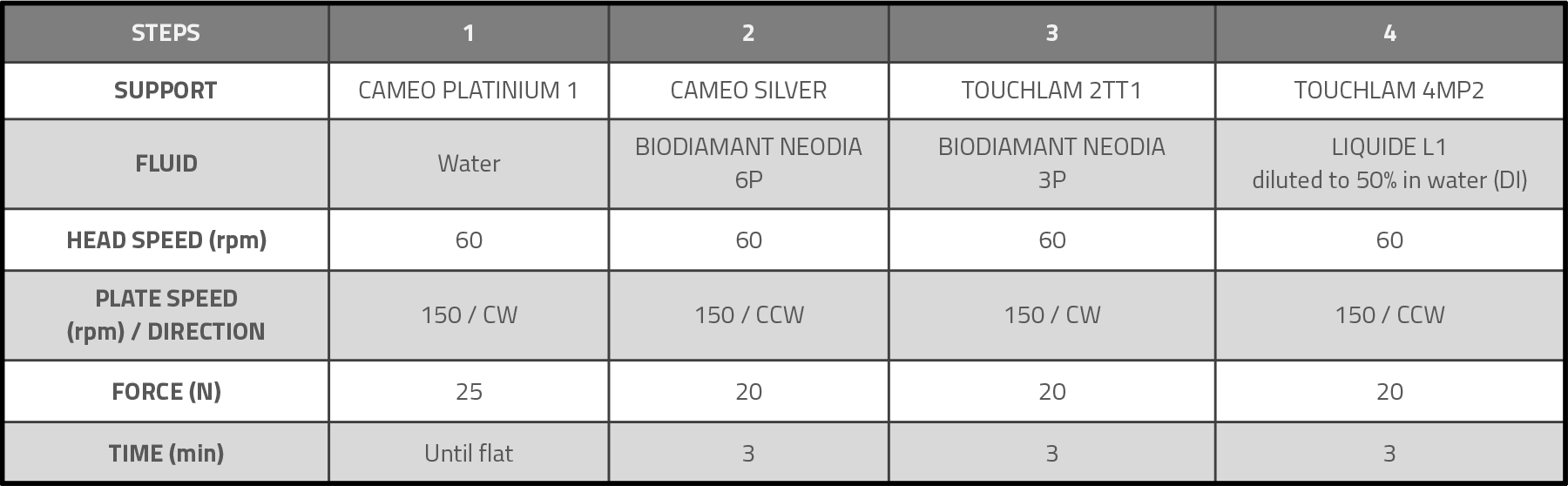
Stähle
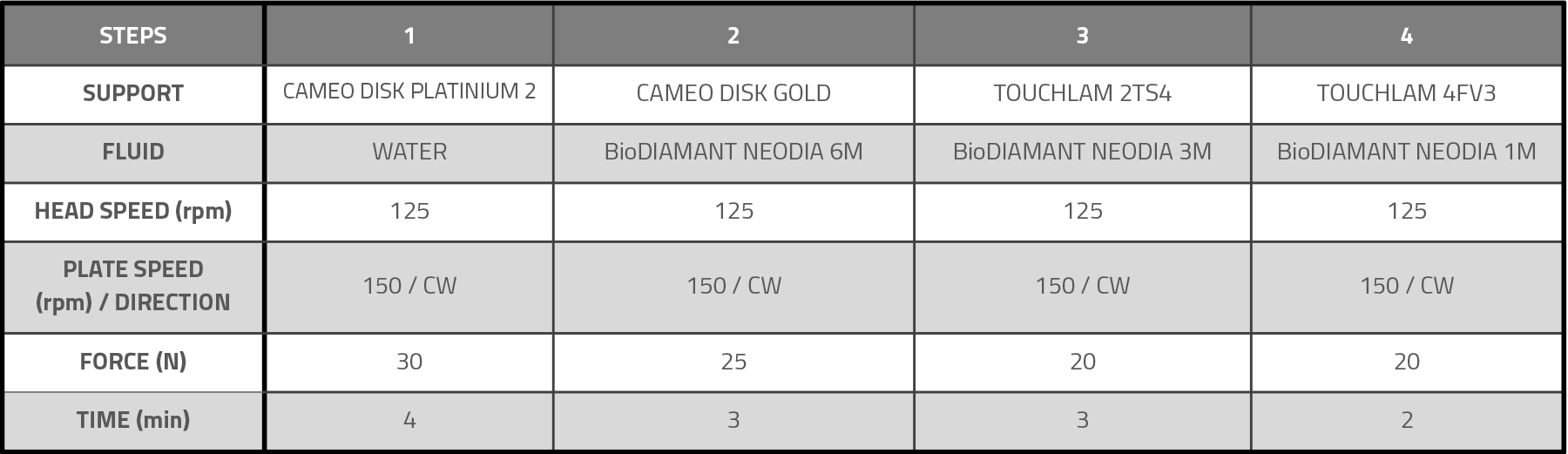
H – Uhrzeigersinn / AH – Gegenuhrzeigersinn / KOPFRICHTUNG: Immer H (die Einstellungen sind optimiert, um 6 Proben mit einem Durchmesser von 30 mm zu polieren).
Tipps zu den Polierschritten finden Sie in unseren Artikeln über die Metallografie bestimmter Materialien :
3/ Probleme und Lösungen
Im Folgenden finden Sie einige Lösungen für häufig auftretende Probleme, die bei der Vorbereitung materialografischer Muster von Teilen, die mithilfe der additiven Fertigung hergestellt wurden, auftreten können.
-
Verbrannte Schnittfläche
-
Ursache(n)
• Zu schneller Vorschub der Disk
• Scheibe nicht geeignet
• Unzureichender Schmiermittelfluss -
Lösung(en)
• Reduzieren Sie die Vorschubgeschwindigkeit.
• Das Fluid im Bereich des Trennens richtig positionieren
-
Kratzer bleiben nach dem Polieren zurück
-
Ursache(n)
• Verschmutzte Polierscheibe
• Unsauber gereinigte Proben zwischen den einzelnen Polierschritten.
• Spalt (Schrumpfung) zwischen Einbetten und Probe -
Lösung(en)
• Ersetzen Sie die Polierscheibe. Bewahren Sie die Polierscheibe in einem geschlossenen Schrank/BoxLam auf.
• Spülen Sie die Proben nach jedem Polierschritt gründlich ab. Verwenden Sie vor dem abschließenden Polieren eine Ultraschallwanne.
• Probieren Sie Epoxidharze aus, um Schrumpfung um die Probe herum zu vermeiden.
-
Chemischer Angriff nicht homogen
-
Ursache(n)
• Das Reagenz ist nicht das richtige
• Abstand (Schrumpfung) zwischen Einbetten und Probe -
Lösung(en)
• Verwenden Sie das richtige Reagenz und die richtige Technik (Ref. ASM Handbook).
• Probieren Sie Epoxidharze aus, um Schrumpfung um die Probe herum zu vermeiden.
-
Verkrustete Schleifmittel nach dem Polieren
-
Ursache(n)
• Übermäßiger Gebrauch von Schleifflüssigkeit
• Übermäßige Kraft beim Polieren
• Falsche Schleifflüssigkeit -
Lösung(en)
• Die Häufigkeit der Dosierung von Schleifmitteln verringern.
• Reduzieren Sie den Druck beim Polieren.
• Prüfen Sie, ob Sie die richtigen Verbrauchsmaterialien verwenden
-
Verschmutzung/Spuren auf der Oberfläche
-
Ursache(n)
• Schlecht gereinigt oder nach dem Polieren schlecht getrocknet
-
Lösung(en)
• Alkohol zum Reinigen verwenden.
• Trocknen Sie die Oberfläche gut ab.
• LAM15 zum Abwischen verwenden
-
Unklare Formen der Porosität
-
Ursache(n)
• Polierzeit auf einer Polierscheibe zu lang
-
Lösung(en)
• Die Zeit für das Polieren mit kolloidalem Siliziumdioxid verkürzen